Outil assez méconnu car son utilité est peu courante, le « gappage » des segments de pistons est rarement à faire mais il est important de vérifier si il faut le faire pour éviter de gros problèmes !
A quoi ça sert ?
Les segments de pistons ont un écartement « gap » une fois en place dans le piston/cylindre. Ce gap a besoin d’être important suivant la préparation du moteur, que ce soit un atmo, turbo, compresseur, qu’il tourne avec ou sans méthanol ou NOS etc… En fait c’est simplement une question de température de combustion qui derrière va réduire le « gap » des segments parce qu’ils vont s’étendre avec la température.
Il est impératif de ne pas se retrouver avec un segment ou ses extrémités viennent en contact, autrement dit le « gap » n’existe plus. C’est là ou les pistons cassent au niveau des entre segments.
Certains segments sont déjà prêts à monter à leur réception, ils sont fabriqués d’office pour avoir un « gap » prévus à un diamètre de cylindre bien précis, on alèse le bloc à ce diamètre et pas besoin d’ajuster le « gap ».
Pour d’autres, les segments sont volontairement fabriqués avec un « gap » serré car ils sont à retailler pour permettre à l’usineur/préparateur d’aléser le bloc à un diamètre choisi et pour une utilisation bien précise.
Dans les deux cas, c’est précisé par le fabriquant des segments.
On en vient à l’utilité de l’outil, cette meule permet de grignoter la matière des segments pour ajuster le « gap » à son besoin. Mais il y a plusieurs types de meules, manuelles, électriques avec des résultats bien différents !
Les modèles que j’ai testé :
Première meule que j’ai acheté, une basique manuelle assez courante, celle-ci a beaucoup de variantes de marques, trouvable sur beaucoup de sites.
Elle est simple à monter, mais elle est manuelle, c’est pas pratique car il faut tenir le segment d’une main, et tourner la manivelle de l’autre. Sachant qu’on peut pas la tourner vite donc c’est long, et tenir le segment d’une seule main fait qu’on peut rapidement foirer un segment !

Je l’avais achetée en connaissance de causes, mon but était de la motoriser, j’y suis arrivé en utilisant mon tour.
Mais j’étais pas fan du disque de la meule, les faces abrasives n’étaient pas régulières alors je le suis fait une installation avec une petite disqueuse, en réutilisant le support de la meule à segments.
Mais rien de tout ça ne m’a convenu, le résultat n’était pas celui que j’attendais car il ne respectait pas certains principes de géométrie. La facilité d’utilisation n’était pas non plus au rendez-vous, donc j’ai revu ma copie et fabriqué une base en partant de rien.
Le comparateur est là pour avoir une indication de l’épaisseur de matière retirée, c’est pas super précis car ça vibre, mais c’est toujours mieux que rien.
La pince pour serrer le segment sur l’outil.
La base ou le segment est fixé est pivotante, le but est que l’on meule le segment autour de son axe central pour que la face meulée soit toujours coïncidente avec le centre du
J’ai découpé des disques de papier de verre que je mets contre un disque à tronçonner, pour avoir une finition de meulage plus fine et avoir un contrôle de la vitesse de ponçage.
J’ai pas de vidéo de mon outil, mais il s’inspire de ce genre de machine que l’on peut acheter toute prête :
Cet article t’a apporté des informations, des idées ou inspiré ?
Fais un don pour continuer de profiter du contenu de ce site.
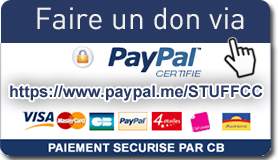
Jolie poste , du coup tu préconise combien pour les pistons forgé sur sr20 ?
J’aimeJ’aime
J’ai juste suivi les préconisations du fabriquant de pistons que j’ai pris. Il faut beaucoup d’expérience pour jouer avec cet ajustement.
J’aimeJ’aime